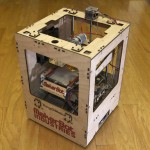
[Update: Welcome back, Slashdot! ๐ This site is in full lockdown mode, so comments may take a little while to appear, but please leave them anyway! You may also want to check out the previous assembly photos also featured on Slashdot.]
Overview
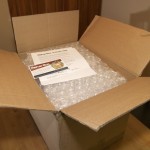
After a couple months of girlish waiting, my DIY Makerbot Thing-o-Matic kit arrived in December 2010. Pictures of the laborious assembly process went up several days after, and have been viewed by tens of thousands of people in the last few weeks alone. Makerboot does not ship a printed manual with the machinery kit, instead option for an online-only “Thing-o-Matic Assembly Instruction/Users Manual”: a living collection of wiki pages that is continually updated. A good thing, indeed! Take a look at the assembly pictures if you haven’t already gotten a feel for the level of assembly effort. (If you’re good with your hands, allocate about 16 hours.)
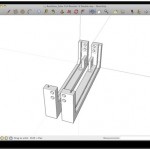
Once the machine is assembled, you’re ready to install the software, connect the machine via USB, and calibrate the system. Rough high-level steps are as follows:
- Install the Arduino driver, if not already installed. (Easy)
- Download and run ReplicatorG, and try making a software connection to the machine. (Easy. You’ll spend a lot of time in ReplicatorG.)
- Use ReplicatorG to manually control all the machines widgets, and test each one for proper function. (Medium.)
- Measure the the Z-axis height and change an obscure config file in your ReplicatorG software that you won’t understand for a few more days. (Medium.)
- Load up some plastic filament. (Easy.)
-
Skeinforge interaction can be a frustrating chore. Within ReplicatorG, launch the embedded Skeinforge configuration application, which is used to take 3D design files in .STL and “slice” them in tooling paths that a machine can follow. This is necessary since 3D printers usually print in layers, starting with the lowest. Skeinforge is an extremely configurable system with an extremely shitty GUI. It is not immediately clear what most of the hundreds of settings do, and you’ll spend many trial iterations configuring options to dial in the best general settings. Even after calibration, you will need to periodically revisit Skeinforge to address build-specific issues. (Hard.)
-
ReplicatorG build platform positional and orientation. Perfect! Use ReplicatorG to either upload a compiled .S3G files to the on-board SD card for disconnected printing, or stream the commands on the fly. (Easy.)
- Run the test job! (Medium.)
- Go to #6. (Daunting.)
The workflow is initially very daunting and cumbersome. It starts to make more sense after a while, but needs major work. This is technically not Makerbot’s issue, but given that it’s a necessary component of the overall system I would suggest major effort be placed in unsuckifying the interaction before ReplicatorG and Skeinforge.
- 3D design software package such as Google SketchUp (free), which is used to design your own objects. Once you’ve designed an object, you export an STL file that is imported into ReplicatorG, which is then sliced by Skeinforge into .gcode files and then by ReplicatorG into .s3g files that the Thing-o-Matics onboard Arduino understands.
- ReplicatorG (and included Skeinforge application), tweaking, compiling, and babysitting.
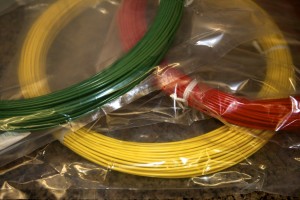
- Extremely cool. You will almost definitely be the only kid on the block with this toy.
- Makerbot maintains the Thingiverse: a user-driven database of open source 3D objects.
- Semi-automated batch jobs via the included Automated Build Platform.
- All needed parts and come with the kit. (BYO tools.)
- Supplies (such as ABS) are also available from Makerbot.
-
Some parts, such as this pair of brackets printed simultaneously, need trimming and/or sanding. Documentation is 4 of 5. The 5 is for comprehensiveness and getting me through the process, but -1 for ocassionally erronous images, ambiguous text, or omission of step.
-
Minimal soldiering, and much less than I’d anticipated.
- Minimal number of “only one chance” assembly instructions such as cutting and gluing,
- Open Source hardware design. You can print many of your own replacement parts if some break.
- Science!
- Generally not robust enough to run unattended.
- Post assembly calibration gets fuzzy, as there is no 100% Right Way to do things.
- I’m 90% sure that something about the Arduino driver is unstable. I regularly make my entire Mac greyscreen (the OSX equivalent of a Windows BSOD or a Linux kernel panic) during plug/unplug process of connecting/disconnecting the USB from the Makerbot to my computer. Something, somewhere, is dying a horrible death and taking my whole operating system with it.
- Skeinforge–the software that converts your 3D models to tool paths–has an absolutely atrocious (and ofter unstable) user interface. Few of the 100+ configuration options are clearly documents within the app, which is buggy to start with.
- The machine can be somewhat loud and obvoxious. In my case, the XY axes aren’t bad, but the Z axis stepper motor can be very irritating.
- If you do this, you are making a very big time commitment.
- Questionable electronic sub-component failure rates, and one of my biggest complaints. The motor on my MK5 Plastruder was dead on arrival, and my power supply went out after less than a dozen prints. I could just be unluckly, though.
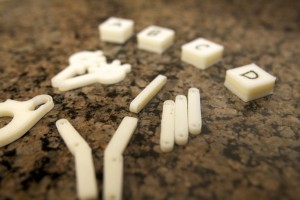
Many small pre-fab printer shops have materialized in the last couple years, ranging from laser-cut wood frames (such as Makerbot), to clear acrylics, metals, and, of course, printed plastics. Regardless of your chosen path, the electronic components are currently not printable in any high-quality manner, are best purchased from a vendor. This includes mainboard microcontroller (the Thing-o-Matic uses as Arduino MEGA), stepper motor controllers, stepper motors, power supply, end stop sensors, extruder controller, cables etc. You can, of course, build these yourself, but in the case of highly available parts such as the Open Source Arduino, it’s far more cost effective to buy the $30 part than spend a day manually fabrication a PCB and hand soldier $20 of mail-order components.
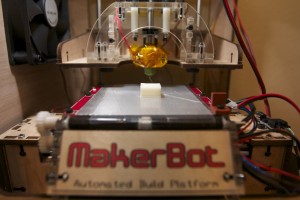
In short, unless you have a Richard Stallman-level of commitment to F/OSS, try to buy all your components from only a few vendors. Makerbot is a good choice for U.S. buyers as though they only sell their own designs–a good thing, IMHO–but then, they don’t sell RepRap parts. If you want a RepRap, the choice is more difficult. I have not built a RepRap, but suspect that even with a larger vendor ecosystem it would be difficult to bring the total price tag for a laser cut or milled non-clone machine to under $1K for quality parts, electronics and components.
- Documentation: 4 of 5
- Ease of Use: 3 of 5
- Coolness: 5 of 5
- Price Competitiveness: 4 of 5
- Support: 5 of 5
- Quality: 3 of 5
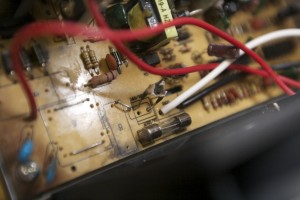
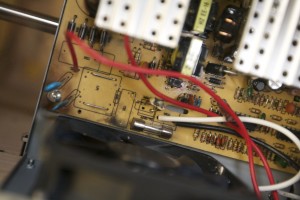
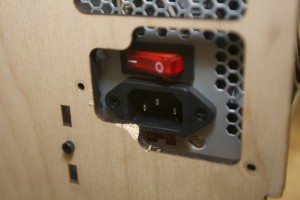